Méthode TPM, ce qu’il faut savoir
la méthode TPM assure l'instauration de la propreté et de l'entretien sur tous les postes de travail.
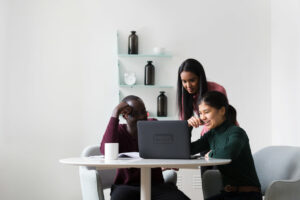
la méthode TPM assure l'instauration de la propreté et de l'entretien sur tous les postes de travail.
Afin d’avoir une production optimale sans à des investissements de moyens supplémentaires, il existe une solution appelée méthode TPM ou Total Productive Maintenance. Grâce à cette technique, les risques des pannes et d’arrêts des équipements liés à la production seront réduits et ainsi permettre une disponibilité optimale des moyens de production. Outre l’amélioration de la qualité et de la productivité, cette méthode TPM permet aussi d’optimiser les indicateurs de performances de l’entreprise.
Par définition, la TPM est une pratique qui a pour but de garantir l’efficience au sein du service de production. Avec l’application de cette technique, le système de maintenance va passer d’une stratégie de traitement curatif à une stratégie de prévention. De ce fait, cette méthode consiste à établir une politique visant à atteindre une amélioration continue des équipements de production.
Ses origines
Issue du Japon, la technique TPM peut être décrite comme un processus de maximalisation des performances. Surtout exploitée dans le secteur industriel, elle est déterminée à partir d’une analyse des problèmes et dysfonctionnements des matériels de production. En 1989, le Japan Institute of Plant Management a instauré la démarche TPM afin d’aboutir à une meilleure performance industrielle. Ainsi, la Total Productive Maintenance est une marque déposée par le groupe JIPM.
Quels sont les objectifs de la TPM ?
Il faut savoir que l’objectif de la TPM est non seulement de corriger, mais également de d’améliorer la productivité d’une l’organisation. Focalisée sur les moyens de production, cette pratique repose aussi sur des indicateurs de performance tel que le TRS (Taux de rendement synthétique). À l’aide de ces résultats, les managers auront un rapport précis de la performance des activités de production et ainsi décider des actions d’amélioration à lancer.
L’indicateur TRS
L’indicateur TRS ou parfois appelé TRG (Taux de rendement global), mesure tous les paramètres qui risquent d’impacter le rendement des opérations. Grâce au TRS, il sera plus facile de déterminer les causes principales de non-performance : la qualité, la disponibilité des équipements ou la performance de production.
Dans un premier temps, la méthode TPM assure l’instauration de la propreté et de l’entretien sur tous les postes de travail. Vu qu’elle met en valeur le suivi des équipements et l’amélioration de l’environnement interne, l’organisation sera plus ordonnée. Bien entendu, les pertes de temps n’affecteront plus la productivité de l’entreprise.
Ensuite, il ne faut pas oublier que la TPM consolide la relation entre l’ensemble du personnel (Maintenance, production, Qualité…) En effet, la communication entre les services sera plus efficace. Pour que le progrès ne s’arrête pas, les habitudes de chacun seront également remises en cause. Enfin, l’avantage de cette technique est qu’elle permet de garantir le respect des règles collectives et des engagements.
Pour information, la TPM se repose sur une fondation (la propreté, l’ordre et la discipline : les 5S) et huit piliers :
Sachez que la réussite de la méthode TPM dépend de l’implication de tous les acteurs de l’entreprise et du respect de ces 8 piliers.
Ça peut vous intéresser
Tous les articlesLe Lean Management, initialement développé pour le secteur manufacturier, est désormais largement adopté dans divers secteurs, y compris celui des services. En se concentrant sur l’élimination des gaspillages et l’amélioration continue, le Lean Management offre des opportunités significatives pour optimiser les opérations, améliorer la qualité du service et accroître la satisfaction des clients. Cet article […]
Le Lean Management est une méthodologie centrée sur l’élimination des gaspillages et l’optimisation des processus pour maximiser la valeur pour le client. Depuis son origine dans l’industrie automobile japonaise, le Lean a été adopté par des entreprises du monde entier, dans divers secteurs, avec des résultats impressionnants. Cet article analyse plusieurs cas réels d’entreprises ayant […]
SMED ou Single Minute Exchange of Dies en anglais, pour changement rapide d'outillage, est une méthode qui vise à diminuer le temps de changement d'outils de production et de réglage entre deux séries.
Demande de devis
Un projet de formation ? Demandez votre devis
Service gratuit
Téléchargement du catalogue